Standalone PDM Preset
Introduction
The Link Razor Power Distribution Module (PDM) is a software-configurable device that replaces traditional fuses and relays. Installing a Link Razor PDM can create cleaner wiring and give additional control that traditional fuses and relays do not have. Link Razor PDMs can be complex to set up so, to simplify the process, base configurations have been created for common PDM installations.
This example uses half of the user configurable pins as outputs. and half as inputs. The output pins act as “relays” connecting the output pins to battery power when the corresponding input pin is signaled. An input is assigned to a kill-switch that cuts power to all the outputs. This preset can be a great starting point for a simple setup in a kit car or track car, and can be triggered by physical switches, or a stock factory ECU for example. The preset can be changed at a later date if you wish to get a CAN keypad or an ECU with user configurable CAN to control it, and re-assign all 12 pins to be outputs.
In this article, you’ll find a list of what you’ll need, how to load this Preset onto your Razor PDM, how you’ll wire this Preset up, and lastly, more technical information should you need it, such as current limits, and explanations around the logic programmed into this Preset.
Bill Of Materials
Component | Amount | Location |
---|---|---|
Link Razor PDM | 1 | |
PDM Circuit Breaker Configuration | 1 | |
PDM Loom | 1 | (26 Pin Superseal connector included with every Razor PDM) |
Wiring Diagram & Pinout
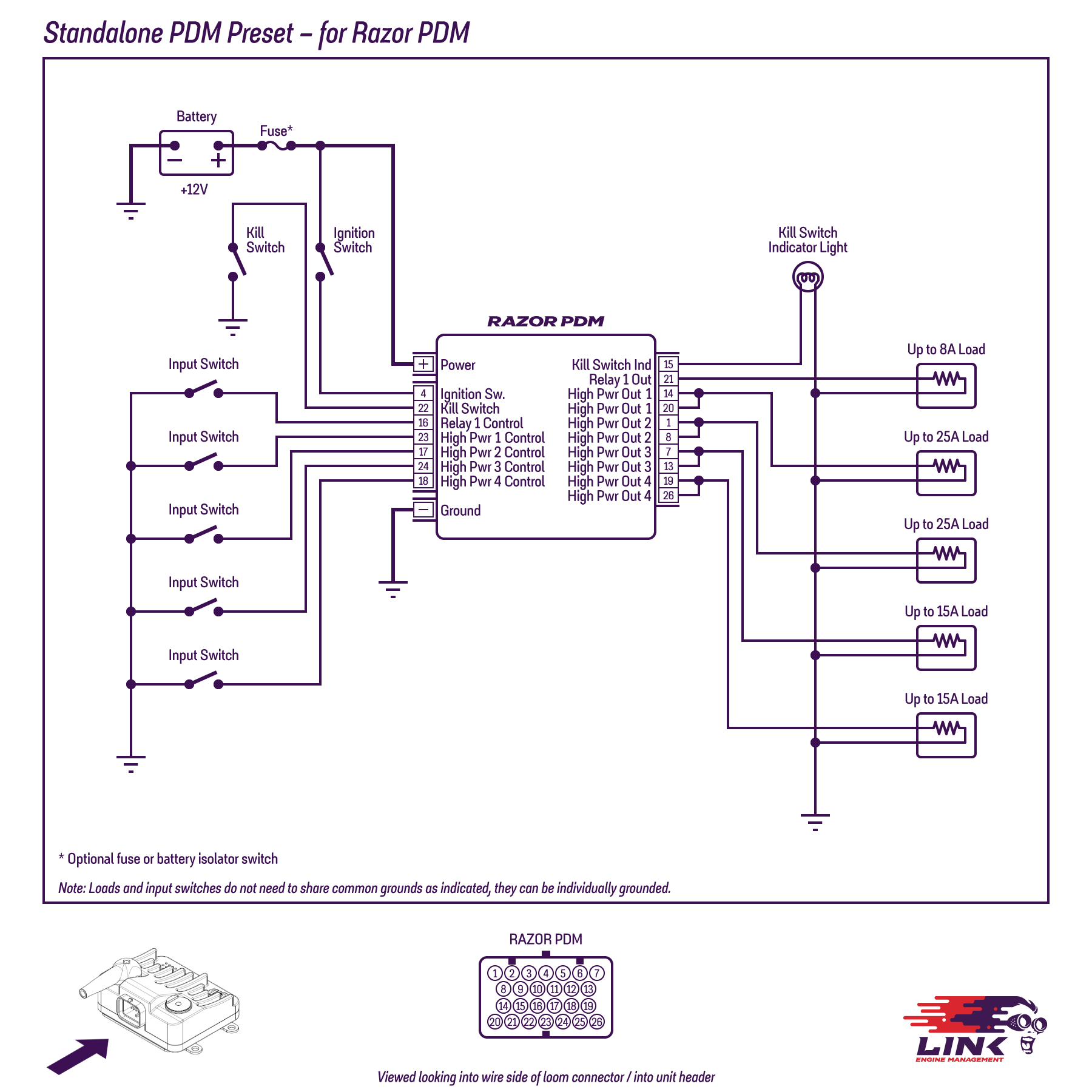
Figure 1 - Wiring diagram for the Standalone PDM Preset for Razor PDM
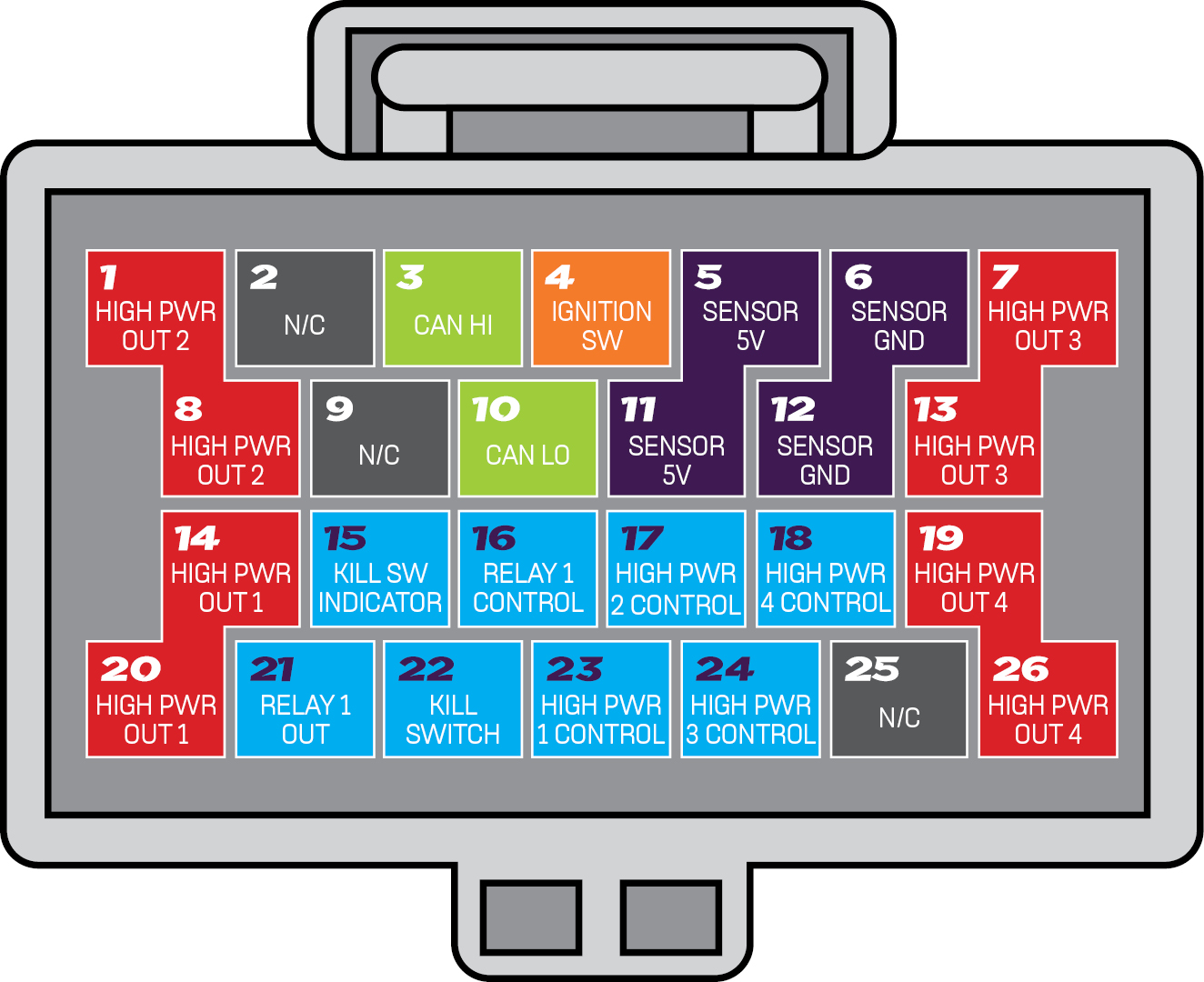
Figure 2 - Pinout for the Standalone PDM Preset for Razor PDM
Loading the Preset Configuration
Ensure your PDM is up to date by following the steps outlined here
By default, the Link Razor PDM comes with a blank configuration and needs to have either a configuration loaded onto it or a new configuration setup from the blank one. The configuration file for this example can be found in the bill of materials section above. Once your chosen Preset is downloaded, you can load this file into the PDM following the instruction set below.
The configs are normally kept in your PDMLink folder, under Configurations, but you can save them anywhere you choose.
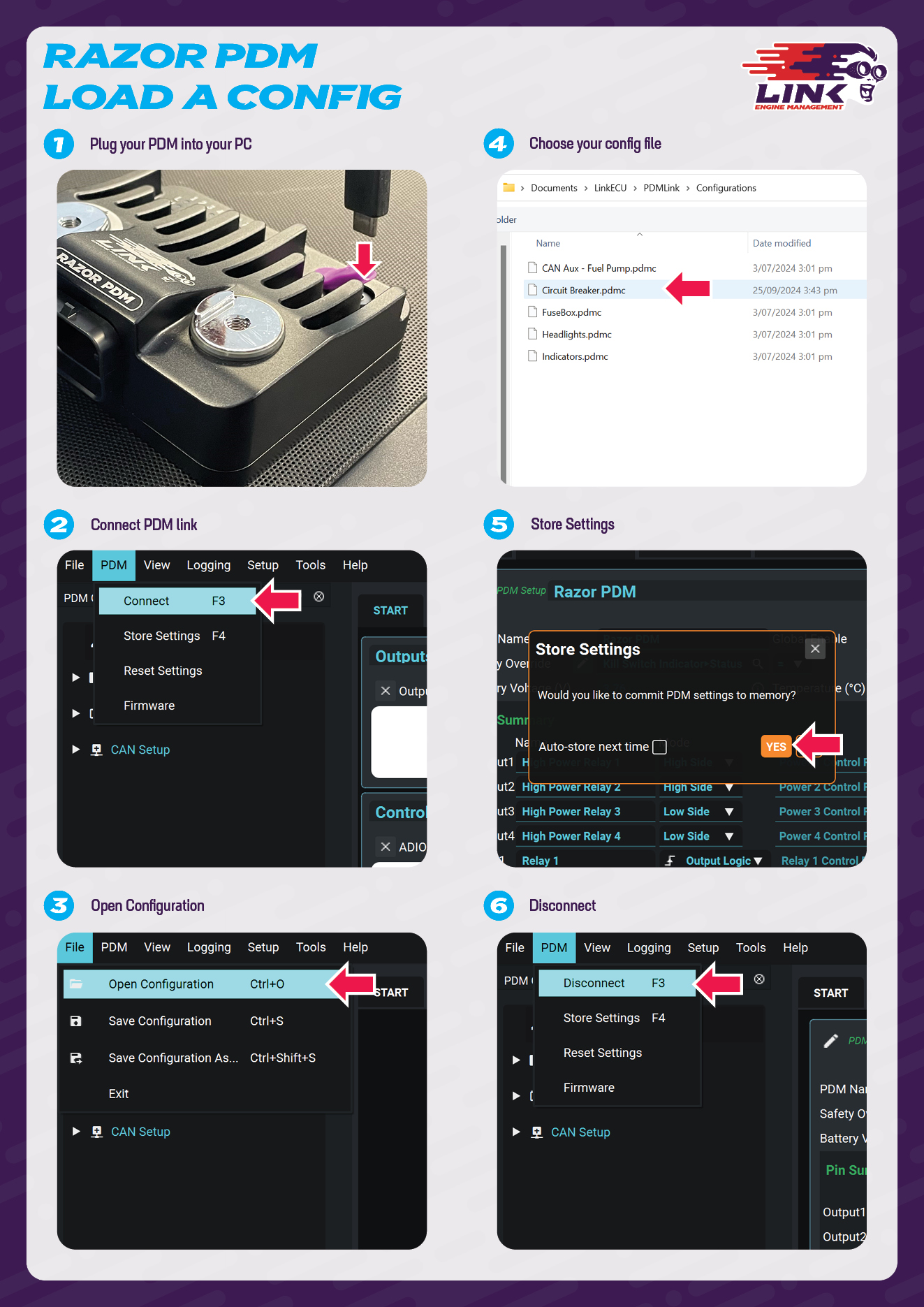
Connect the Link Razor PDM to a computer via the supplied USB C to USB A cable. Note the PDM does not need to be wired into any external power for this step and can be configured purely over USB power.
Open PDMLink and click PDM > Connect, or press F3
Once the PDM has connected, click File > Open Configuration, or Ctrl+O
Navigate to the directory that you saved the Preset to, and select it.
When the app prompts you to store the data on the device, select ‘Yes’.
Disconnect the PDM from the app and PC.
Feel free to review the Preset configuration in PDMLink before disconnecting. You can use Presets as they are or as a starting point, customising them with your own logic and automation to meet your specific needs.
Circuit Breaker Setup Information
ADIO Pins
ADIO pins are configurable pins that can act as analogue i.e. voltage signals from 0 - 5 volts, or digital i.e. PWM Signals. The pins can either act as inputs for these analogue or digital signals or output these analogue or digital signals.
Inputs
Of the 8 ADIO pins on the Razor PDM, 6 are being used as analogue inputs. The input pins can have a pull up resistor enabled to pull the sensor to 5V. Three of the analogue pins have this enabled by default for the two high power inputs and the kill switch. When an input of these get grounded, the designated output gets activated. Note: This means these inputs will show active when they aren’t enabled. This was done so the switch doesn’t have to have a power source attached.
The Kill switch functionality is set up on the Configuration tab in the safety override section. The safety override sets a pin, or set of pins into the fault state when a certain condition is met. A pins safety override functionality can enabled or disabled on it's corresponding tab in the layout. In this preset all the output pins are set up to use the safety override function. So when the safety override condition is met the output pins ( High power output 1, High power output 2, High power output 3, High power output 4 and Relay 1) will go into a fault state and their designated front LED’s on the PDM will go red. This fault state disables the output pin.
The pin will change state to active when the sensor reads voltage over the high threshold value for the assigned duration time, and go inactive when the voltage goes below the low threshold for the allotted duration. When the voltage is between the high and low threshold the pin will keep the status it had previously. i.e. if the pin status starts as inactive and the voltage goes above the low threshold the pin will stay inactive until the voltage is above the high threshold value for the duration.
Input Specifications
Input Name | Pin Name | Input Mode | Pull up | High Threshold | High Duration | Low Threshold | Low Duration |
---|---|---|---|---|---|---|---|
High Power 1 Control | ADIO 5 | Analogue | Yes | 4.50 | 0.01 | 4.50 | 0.01 |
High Power 2 Control | ADIO 6 | Analogue | Yes | 4.50 | 0.01 | 4.50 | 0.01 |
High Power 3 Control | ADIO 7 | Analogue | Yes | 4.50 | 0.01 | 4.50 | 0.01 |
High Power 4 Control | ADIO 8 | Analogue | Yes | 4.50 | 0.01 | 4.50 | 0.01 |
Relay 1 Control | ADIO 4 | Analogue | Yes | 4.50 | 0.01 | 4.50 | 0.01 |
Kill Switch | ADIO 3 | Analogue | Yes | 4.50 | 0.01 | 4.50 | 0.01 |
The safety override is a crucial feature of this preset, for easy control of the PDM’s outputs. The configuration option for the safety override can be found in the PDM setup on the configuration tab. In this preset the panel is set up to activate when the kill switch indicator is active. The kill switch indicator goes active when the kill switch pin is inactive / pulled low. The high power outputs and relay 1 is set up to listen to the safety override functionality.
GP Functions
GP functions have a configurable output pin and certain activation conditions. The GP functions in this preset are being used to “link” the input pins status to the output pins status. The input and output pins all have inverse relationships (input pin inactive for output pin active).
Using the preset
The 4 high power and 2 of the ADIO pins are set up as outputs. One of the ADIO pins are set up to output a signal designed to power a 12 volt bulb (kill switch indicator). This bulb is turned on when the kill switch input is grounded. The other outputs are each assigned an input pin and these outputs supply power when the designated input is triggered. For the High power outputs and the relay output, the input pin trigger is being grounded.
Output Specifications
Output Name | Pin Name | Relay Number | Type | Mode | Inrush Limit (A) | Inrush Trip Time (s) | Inrush Duration (s) | Overcurrent Limit (A) | Overcurrent Trip Time (s) | Retry Limit | Retry Delay (s) | Temperature Limit (°C) |
---|---|---|---|---|---|---|---|---|---|---|---|---|
High Power Relay 1 | Output 1 | 1 | High Power | High Side | 60 | 0.5 | 2 | 25 | 2 | 5 | 1 | 90 |
High Power Relay 2 | Output 2 | 2 | High Power | High Side | 60 | 0.5 | 2 | 25 | 2 | 5 | 1 | 90 |
High Power Relay 3 | Output 3 | 3 | High Power | Low Side | 25 | 0.5 | 2 | 15 | 2 | 5 | 1 | 90 |
High Power Relay 4 | Output 4 | 4 | High Power | Low Side | 25 | 0.5 | 2 | 15 | 2 | 5 | 1 | 90 |
Relay 1 | ADIO 1 | 5 | Low Power | Output Logic | X* | X* | X* | 8** | 2 | 5 | 1 | 90 |
Kill Switch Indicator | ADIO 2 | 6 | Low Power | Output Logic | X* | X* | X* | 8** | 2 | 5 | 1 | 90 |
*These values aren’t applicable for ADIO outputs
** The Overcurrent limits cannot be configured for low power IO.
Inrush Current
When some loads are initially turned on, they require much more current than normal. To handle this issue, High-Power outputs have a higher current limit of X.XA for the first 2 seconds of use. During this time, the output is not allowed to go over the increased current limit for more than 0.5 seconds. If it does, the output will turn off and go into a fault state. After 2 seconds of operation, the output will use the lower overcurrent limit of X A.
Continuous Current
The continuous overcurrent limits for output are shown in Table 2. All outputs' continuous overcurrent limits can be exceeded for 2 seconds. Afterwards, if the output still detects an overcurrent, it will go into a fault state. See Table 2 for further details on High-Power output specifications.
Fault Recovery
After going into a fault for 1 second, the output will automatically try to turn itself back on again. If an output faults 5 times, it will turn itself off until reset manually by the user. Turning the output off with the keypad will reset its fault count, allowing it to function as normal again.
Temperature Limit
Each output is configured to turn itself off when the board gets hotter than 90˚C to avoid damage to the device. The relay will go into a fault state, just like when it exceeds the current limit. However, the relay will not turn back on until the device’s temperature falls to 88˚C. For optimal thermal performance, it is recommended to keep the Link Razor PDM in an area with airflow and mounted to a large flat metallic surface.
Further information on how to configure a PDM and what each setting does can be found in the PDM Help Manual for PDMs. Additional support and contact information is available on the product support page here.